Fully automated production plants
Together with MFL Faserzement GmbH, we work on fiber cement projects worldwide. Typical for FC plants are the high number of actuators and sensors, the large drives in the raw material preparation, the low cycle times despite large loads as well as maximum plant efficiency. The scope of the plant, the commissioning time as well as the conditions on site are a great challenge for our engineers. Thanks to well-known Swiss values such as quality, efficiency and reliability, we are still able to successfully compete with international competitors and convince with industry leading cycle times.
- control and operating concept for plants with several thousand actuators and sensors
- design of servo and frequency converters up to 560kW
- hardware engineering (in some cases over 80 cabinet panels)
- cabinet manufacturing with worldwide delivery (UL certification)
- software engineering for raw material / cement preparation (refiner control for cellulose, ball mills for silica, cement mixer, etc.)
- software engineering for board machine (thickness control, cutting tables with servo drive)
- software engineering for stacking and transport systems (with servo drive up to 75kW)
- software engineering for high pressure press (synchronous control, press control with up to 16'000 tons press force)
- operating and visualization concept (with touch panel, PC stations or in combination)
- installation supervision on site
- commissioning, production start-up and operator training (usually several months)
Project description
Fiber cement products are widely used especially in humid regions like the Eastern countries, South America or in Eastern Europe. Fiber cement panels are robust, easy to work with and have a long service life. One of the largest projects we have realized was for a customer from Thailand, where four complete process lines were implemented. For each process line, the engineering effort took one man-year and included hardware as well as software engineering for process and visualization. The commissioning period extends over several months and is carried out directly on site. After six weeks of IO testing, the plant starts operation and is optimized step by step to its performance limits. One of the four plants was also equipped with a high-pressure press, which presses water out of the board after production with a pressing force of 16,000 tons. This increases the density and strength of the plate and should meet higher demands after autoclaving. Along the whole line, various PC stations and touch panels are installed to monitor the line, start production recipes and operate the process.
Requirements
- constant plate thickness (+/- 0.1 mm)
- sheet production speed (approx. 150 m/min)
- cycle time stacker and destacker (approx. 10 sec.)
- pressing cycle with recipe
- cellulose preparation with recipe
- mixing with recipe
- simple and user-friendly operation
- robust control system
- registration of several thousand IOs
- fully automatic transport system
- loading & unloading system for autoclaves
- recycling of process water
- raw material silos
- interfaces to further processing plants
Scope of supply
- preparation of the motors and equipment list
- creation of the IT concept
- creation of the operating concept
- recipe controlled raw material preparation with traceability
- motion applications for cutting tables and stackers
- VFC controlled transport systems
- control systems for press cycle
- control systems for drying tunnel
- software engineering for entire process
- plant visualization
- hardware engineering
- cabinet construction and monitoring
- commissioning on site
We would be pleased to demonstrate our expertise and present our worldwide references to you.
We are at your disposal at any time for a presentation of our skills and show you development possibilities for your business by means of some reference projects. We are convinced that, thanks to our many years of experience in various industries, we combine the necessary skills to accompany you profitably.
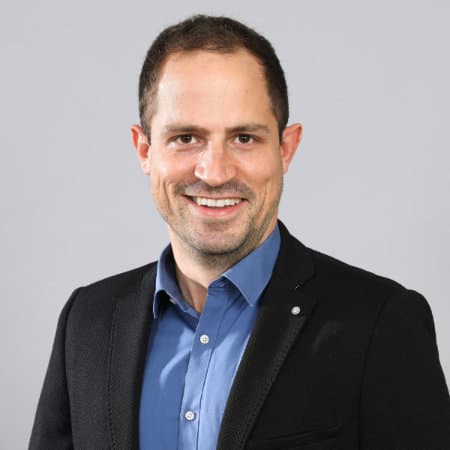