ICS-Control-System for flour mills
ICS Automation AG has specialized in retrofit projects of various kinds for many years. Thanks to the know-how of our employees and the experience we have gained in various industries, we know how to take on new challenges and create added value for our customers. Our customers benefit from our solution-oriented mindset and our customer-specific applications. Our system combines industry-specific standards, which are complemented by suitable concepts and technologies from other industries. As a result, the customer receives a customized mill control system with optimized process visualization, simple process handling and reliable process control.
When developing a mill control system, we focused on the following customer benefits:
- Safe and reliable production (also unmanned)
- Preservation of investments by integrating all existing machines
- Machine manufacturer-independent automation solution
- Reliable, state-of-the-art system, equipped for the future
- Relevant increase in efficiency in some areas of the plant
- Simple and efficient operation
- Improved production overview and monitoring
- Detailed display of information
- Production data available anytime and anywhere
- Tracability throughout the entire system, from receipt of material to the finished product
- Efficient error analysis
- System data available for optimal maintenance
- 24/7 support for the entire system
- Remote access for customer employees
Project description
The milling control system to be replaced at the Stadtmühle Schenk AG, which controls the entire milling process including wheat silo, flour production, mixing and packing/loading, was installed in 2005 and expanded over the following years. The systems include the wheat silo (total of 96 silos with a capacity of 22,000 tons), the flour production (soft wheat mill with 192 tons/24h and special mill with 60 tons/24h), two flour mixer (18 tons/hour & 6 tons/hour capacity) as well as the packaging and loading (total of approx. 100 flour and loading silos). The systems were controlled by 3 PLCs (Siemens S7-400) and a process control system (WinCos R1).
In the final concept of ICS Automation AG, all Siemens S7-400 were replaced by Siemens S7-1517 and the peripherals were optimized to such an extent that only the modules that were really needed were integrated. The system is operated via the system visualization and process control system from ICS Automation AG. Our system combines control system and MES functionalities and thus enables simplified process operation and process monitoring. In order to provide the operator with a maximum overview of the system, the operating stations were designed with a wide screen.
The customer has forced a replacement of the previous control system for the following reasons, among others:
- Upcoming WinCos & operating system upgrades
- Improved support access and assistance
- Shorter response time for requests and upgrades
- Local partner with guaranteed support from Switzerland
- Direct contact persons with knowledge of the plant
- Integration of new machines with Swisca
Requirements
- PLC replacement with the latest generation
- new process control system
- prepared for future MES / ERP connection
- new and simplified process visualization
- takeover of process and machine parameters
- complete traceability through process
- replacement of the existing operating PCs
- short time frames for tests & go-live
- long-term Swiss partner relationship
- 24/7 support for the entire system
Scope of supply
- recording the existing functionality
- recording specific customer requirements
- concept for conversion and go-live phase
- improved tools for traceability
- new control and operating concept optimized for the milling plant
- optimized order handling for unmanned operation
- integration of 10 different Bühler device types
- software development for PLC, PCS and visualization
- set-up of a digital twin
- commissioning & conversion on site
- training and coaching
- production support
- service & support with remote access
Hardware & control
- parallel integration of flow balancers from Swisca
- dismantling of unused devices during the conversion
- clean-up of conversions already carried out
- reuse of the existing hardware incl. Profibus
- > 4500 inputs and outputs (sensors / actuators)
- various device interfaces (Profibus, Profinet, serial)
- replacement of 3 PLCs with Siemens S7-1517-3
- 6 new operating stations with widescreen
- modernization of network and IT, incl. VPN access
- > 25 process lines and 230 silos (wheat & flour)
- audit trail through the entire process
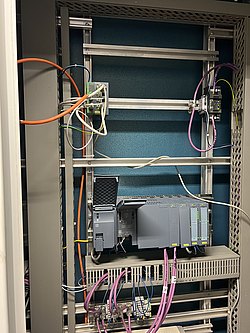
We would be pleased to demonstrate our expertise and present our worldwide references to you.
We are at your disposal at any time for a presentation of our skills and show you development possibilities for your business by means of some reference projects. We are convinced that, thanks to our many years of experience in various industries, we combine the necessary skills to accompany you profitably.
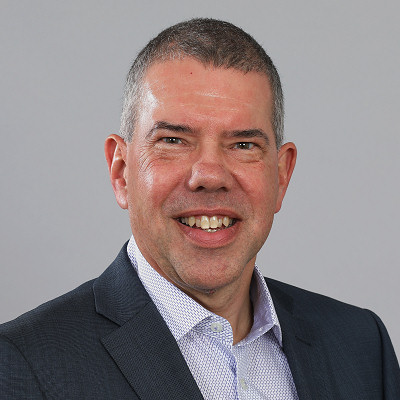