Batchmixer integration
Thanks to the continuous exchange with our customers, we receive frequent requests to develop process optimizations with a focus on energy consumption, sustainability or minimization of downtime and waste.
The project presented below started with the requirement to modernize six existing batchmixers (software & hardware) and to integrate them into the process control system. The mixer sequence now follows a step recipe, which is managed centrally on the process control system. Thanks to various analysis options, traceability and data integrity are ensured.
In the course of the integration, the power consumption and the mechanical load on the mixer are also to be optimized. For this purpose, a low-viscosity dosing component is selected in the recipe, which is dosed in a controlled manner in order to regulate the power consumption of the mixer drive. The following main activities were in the scope of the project
- conversion during running production
- parallel operation of integrated and non-integrated mixers during the modification phase
- implementation of a step handler for process control
- central product-, recipe- and parameter management
- historical production data
- intelligent dosing for output optimization
- recalculation of specific dosing components for final dilution
Project description
The six batchmixers are converted one after the other and integrated into the plant control system. For this purpose, a new Siemens S7 PLC is used, which is connected to the process control system via a bus system. Each mixer receives a new control cabinet with a decentralized I/O node. Thanks to the step-by-step conversion, production can continue without any major disruption. The step recipes for the desired mixing sequence and the associated parameters are now managed centrally in the process control system. On the one hand, this makes it easier to make adjustments and extensions to the recipes, and on the other hand it enables the verification of the batch and step recipes. Thanks to various analysis options, traceability and data consistency are also guaranteed. In the course of the integration, not only the existing functionalities are to be adopted, but additional, more complex functions are also to be implemented. For example, a low-viscosity dosing component can now be selected in the recipe. If the current consumption of the mixing drive now exceeds a defined value, part of this component is dosed and thus the viscosity of the mass is reduced. In this way, the power consumption and the mechanical load on the mixer can be optimized.
Requirements
- replacement of old hardware
- integration into the process control system
improved traceability - central recipe, product and parameter management
- extended functionality of the mixers
- modification during operation
- parallel operation of integrated and non-integrated mixers during the rebuild phase
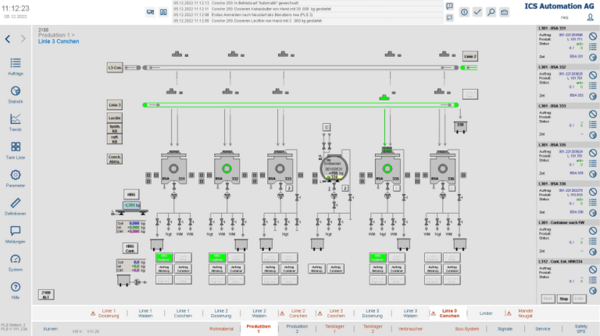
Scope of supply
- recording of customer needs
- workshop and analysis of possibilities
- control system replacement
- integration into the process control system
- integration into the plant visualization
- measures for energy optimization
- implementation of a step handler for the process control system
- optimization of dosing process
- phased commissioning (1x on site, 5x remote)
- service & support with remote access
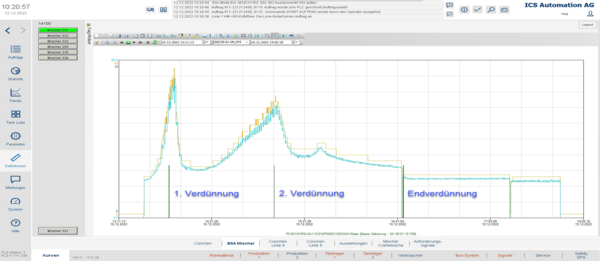
We would be pleased to demonstrate our expertise and present our worldwide references to you.
We are at your disposal at any time for a presentation of our skills and show you development possibilities for your business by means of some reference projects. We are convinced that, thanks to our many years of experience in various industries, we combine the necessary skills to accompany you profitably.
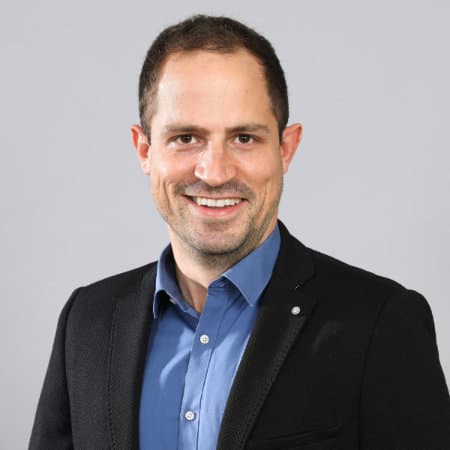