Production line with traceability
The requirements for production companies are continuously increasing. One of the main requirements is the traceability of production processes to ensure food safety. The systematic division of the production process into individual process lines and the subdivision into defined production quantities (batches) form the basis for such traceability. Today's systems offer further possibilities and an almost complete reporting of the production process.
- traceability through the production process
- material and batch handling
- labelling of semi-finished and finished products
- tank farm management
- container handling
- warehouse management
- production recipes and order handling
- reporting and trend curves
- monitoring of operator interactions (audit trail)
- tracing of each sensor and actuator (historian)
Project description
Lindt und Sprüngli France, with the plant in Oloron, faces a special challenge. The steadily growing plant is constantly being expanded and extended with new production lines. The individual production lines are all controlled by autonomous control systems and therefore represent a great challenge, especially for maintenance and operators. Different control types, various bus systems as well as the diverse user interfaces are just a few examples of the high variance. Thanks to the positive reputation in the food industry, ICS Automation AG was finally given the opportunity to help the customer and equip his plant with an ICS process control system. This allows the customer to integrate the existing control technology and processes despite complete modernization and standardization of the operating systems. Thanks to the new user interface, the customer-specific dialogs and reports as well as the uniform PLC programming, he is now perfectly prepared for further expansions.
Scope of supply
- pre-engineering with as-is analysis
- specification of the target concept
- basic concept for control of the entire plant
- basic concept for product traceability
- definitions for tanks, lots, lines
- integration of printer and scanner
- definition of operator stations
- software engineering
- setup of a digital twin
- in-house test with pre-acceptance test
- remote access for 7/24 customer support
- commissioning with process optimization
- implementation of further phases
Hardware & control
- server/client system for operator stations
- standby server with data replication
- WinCC for visualization and operation
- process control with several Siemens S7-400 PLCs
- various PC operator stations for process operation
- barcode reader and on-site HMIs
- ethernet network for IT infrastructure
- profibus network for integration of smart devices
We would be pleased to demonstrate our expertise and present our worldwide references to you.
We are at your disposal at any time for a presentation of our skills and show you development possibilities for your business by means of some reference projects. We are convinced that, thanks to our many years of experience in various industries, we combine the necessary skills to accompany you profitably.
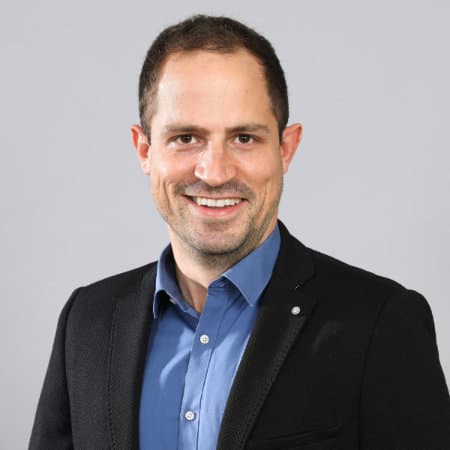